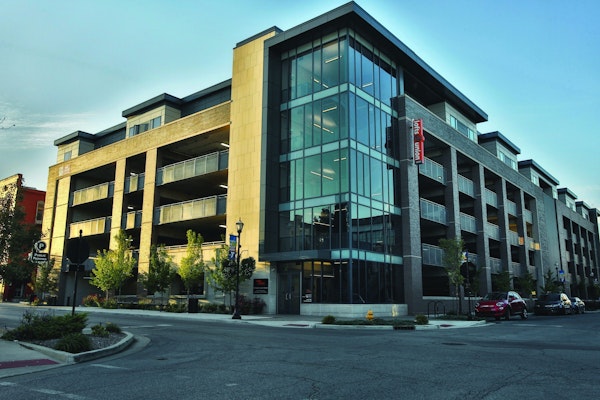
Envoy's Expertise in Cast-in-Place and Pre-Cast Construction Helps Determine the Optimal Solution for Parking Garage Projects
As a construction company, Envoy understands the importance of providing efficient and reliable parking facilities for residents and visitors of towns and cities. When it comes to building a parking garage, there are two options to consider: cast-in-place and pre-cast construction.
Cast-in-place construction involves pouring concrete on site to form the structure of the parking garage. This method allows for more flexibility in design and the ability to make changes during the construction process. Additionally, cast-in-place construction allows for the use of reinforcing steel and post-tension cables to be placed in the concrete, which can lead to a more durable structure that is better able to withstand the stresses of daily use. This flexibility can be particularly beneficial in connected or adjacent mixed-use projects where varying floor-to-ceiling heights may be required. Cast-in-place construction can also allow for more complex architectural features such as curved walls, which can enhance the aesthetic appeal of the parking facility. Additionally, cast-in-place construction typically allows for higher ceilings and fewer spandrels (horizontal beams between floors) as the structure is poured on-site, and this can provide more natural light and a more open feel to the parking garage. However, it also typically takes longer to complete and can be more expensive due to the need for more on-site labor.
When it comes to maintenance, cast-in-place parking garages require regular inspections to check for any cracks or damage in the concrete and reinforcing steel. Regular surface cleaning and sealing can also help protect the concrete from water and salt damage. Additionally, the expansion joints, water drainage systems, and parking surfaces should be checked and maintained regularly to ensure the safety and functionality of the structure.
On the other hand, pre-cast construction involves creating concrete components off-site and assembling them at the site. This method is generally faster and more cost-effective, as the pre-cast components can be produced in a controlled environment with less labor required on-site. However, pre-cast construction is less flexible in adapting to site conditions and architectural features, as it can be more difficult to make changes during the construction process. Additionally, the pre-cast components are relatively thin, so they may be more prone to cracking or other forms of damage over time. Pre-cast garages generally have lower ceiling heights and more spandrels as the components are pre-fabricated and limited by transportation and assembling capabilities.
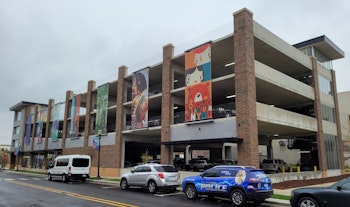
In terms of maintenance, pre-cast parking garages require regular inspections to check for any cracks or damage in the pre-cast components. The expansion joints and water drainage systems must also be checked and maintained regularly. Additionally, the pre-cast components are generally sealed during the manufacturing process, but over time the sealant may degrade and need to be reapplied to ensure the longevity of the structure.
When it comes to value and usability for residents, both options can provide a functional and safe parking facility. However, cast-in-place parking structures are known to require less maintenance, are more flexible in design, and can have higher ceilings and fewer spandrels which can provide a more open and natural light feel to the parking garage. Pre-cast garages can seem tight and claustrophobic at times, and actually, cause users to duck as they drive through. Vibrations can also be felt more prominently in pre-cast garages. This vibration can translate into adjacent or attached buildings.
Both cast-in-place and pre-cast construction have unique advantages and disadvantages. As a construction company, we are experienced in both methods and can work with leaders to determine the best option for their specific project based on factors such as budget, design, maintenance, resident needs, and timeline. We are committed to delivering high-quality, efficient, and cost-effective parking facilities for our customers.
Interested in learning which parking garage project type will fit your needs? We're always happy to go over the best options with you and your team. Contact us today to get started.